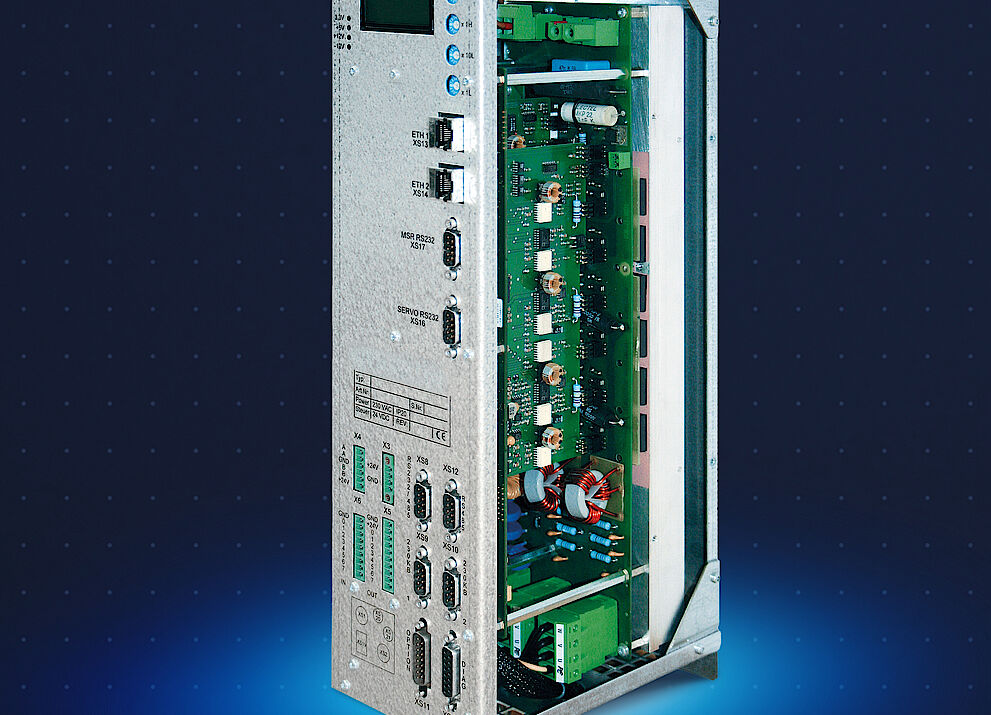
Pressemitteilung
Von einfach bis komplex
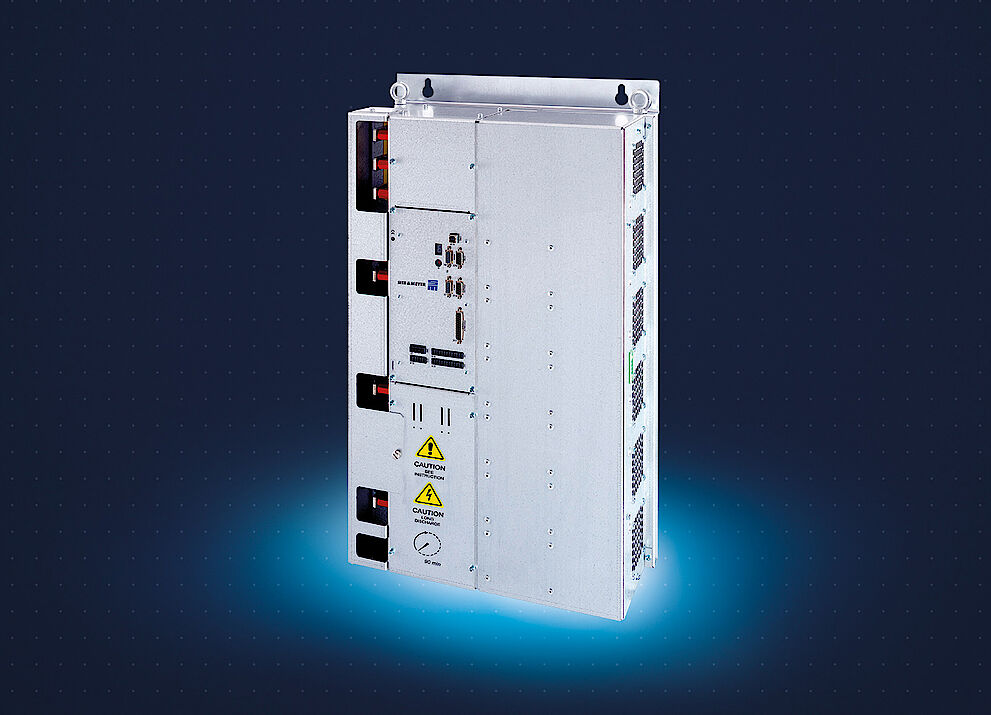
Pressemitteilung
Mehr Power im mittleren Leistungsbereich
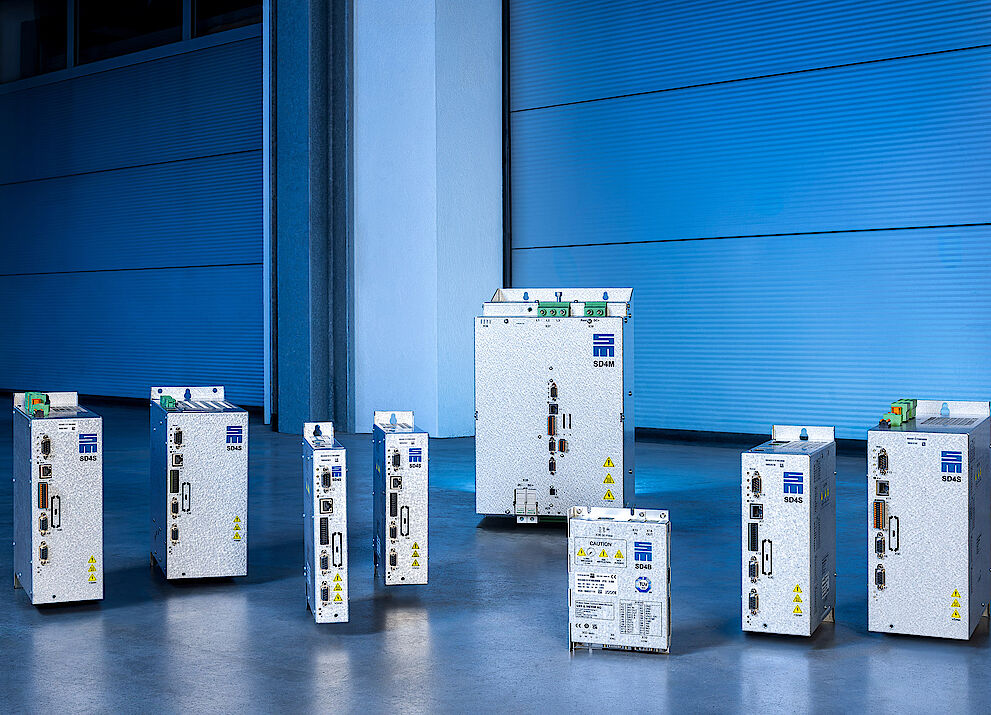
Pressemitteilung
Ein Drive Controller für alle Fälle
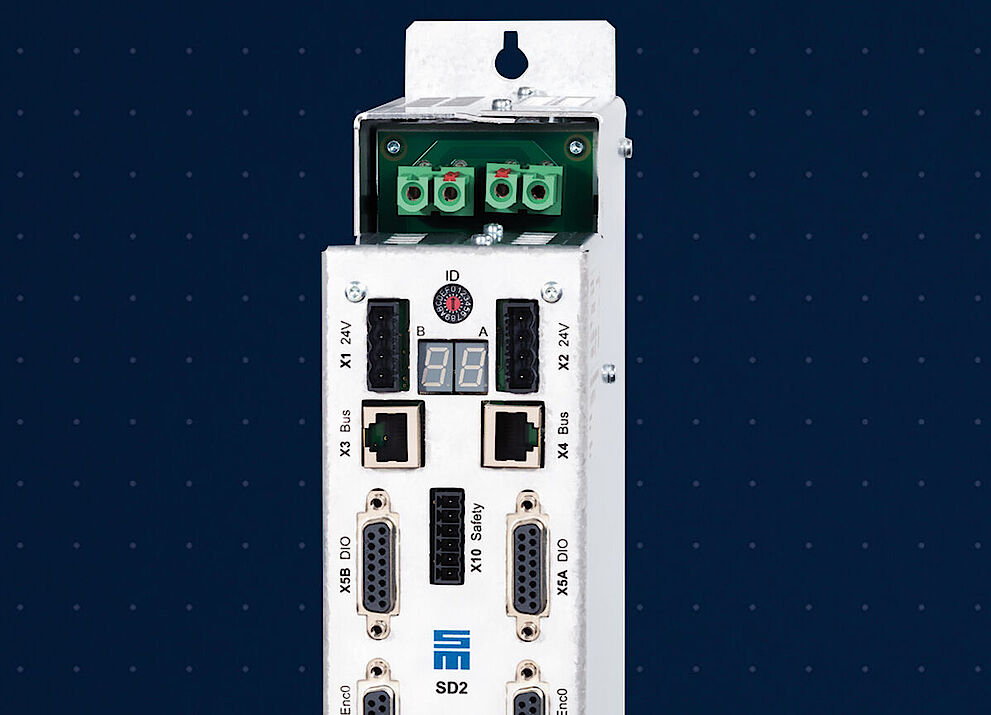
Pressemitteilung
Mehr Effizienz, weniger CO₂
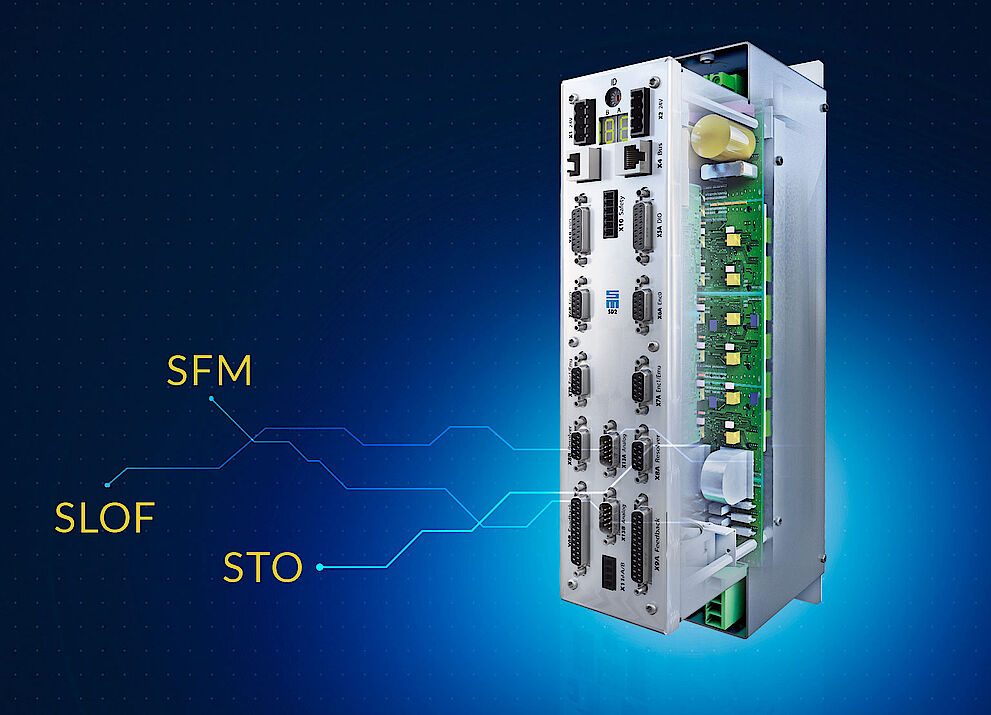
Pressemitteilung
Drive Controller SD2 von SIEB & MEYER mit integrierten Sicherheitsfunktionen
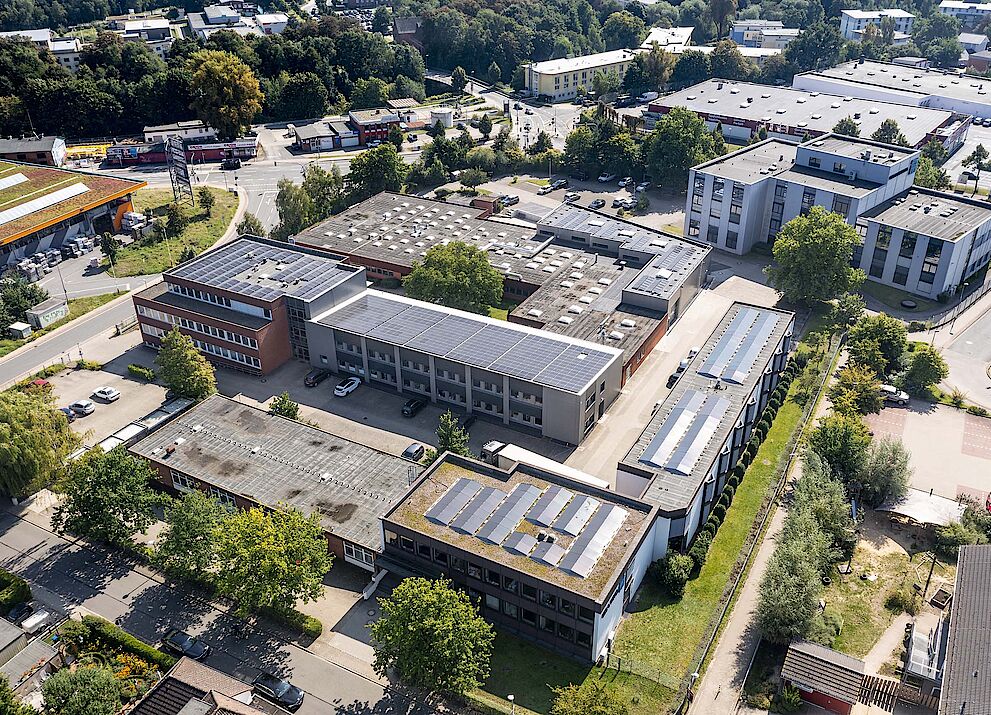
Pressemitteilung
SIEB & MEYER AG steigert Jahresumsatz 2024 um 55 Prozent
SIE BENÖTIGEN WEITERE INFORMATIONEN?
Für weitergehende Fragen steht Ihnen unsere Presseabteilung jederzeit gerne zur Verfügung:
Frau Annika Ritari
Pressearbeit, Media, Messen
Telefon +49-(0)4131-203 - 1381
E-Mail Annika.Ritari @sieb-meyer.de
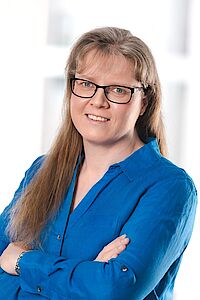